I was just looking to start a project like this after looking at speeduino and seeing nothing really suitable priced sized or as such.
I constantly have issues with the carbs on the kids china mororbikes float bowls sticking fuel leaks cold start and winter summer tuning issues.
I has a few ideas that i thaught might be cool.
I planned to use an Esp32 for remote kill the bike (kids safety)
I also planned to use a rc servo to control the throttle as this will negate the need for tps and Will give you idle speed control.
It will also enable you to govern throttle opening ramp times etc and enable dsg style burp on down shift.
Thie servo cable setup would mean out of the ecu you could provide a cable to the throttle body making it work with stock throttle bodies one would just need to replace the the pipe between the throttle body with a map take off pipe and IAT sensor and injector.
Maybe you could look at adding servo control to your device?
What you’re proposing would be better done as it’s own modification if you feel it’s worth the effort over using normal TPS sensor and idle control stepper. Adding more to the project’s R&D is really unappealing to me right now, enough on the plate as it is.
Before coming across this project, I was planning to build my own unit based of a speeduino as the MS license terms limit custom hardware, but making the system cheap was my goal.
In reality the EFI system is going to be half the cost of the whole bike and if I could get away and just drill and tap an IAT and MAP into the intake manifold it would save some coin.
An RC digital servo would be cheaper than an ISCV/ TPS and a specialist throttle body.
An RC servo only requires 3 wires, 5v (except for the HV versions) and a PWM signal, looking at your Micro you have chosen in your recent posts you have spare timers to work with, it would be little real-estate on your PCB to up your buck boost converter to output higher current to run the servo of the 5v line or pick a HV servo and run it off 12v.
The servo could be integrated into the case of the ECU with just a throttle cable coming out.
At this point it would be simpler than a 4 wire ISCV to implement as that requires high current and two 12 v pwm lines.
What safety features do you propose implementing to ensure that when (not if) your servo or linkage malfunctions, the throttle plate won’t lock in place and cause someone to get hurt?
If those features make sense, what does the cost analysis look like?
Then if it still makes sense, what amount of effort (time and funds) would be necessary to validate your assumptions and the design over a large enough internal test sample to discover and resolve any other potentially problematic failure conditions that were overlooked in the design phase?
Will it pass certification?
Does it make the product uninsurable?
See, it gets complicated.
Something that only costs a few dollars and takes a few hours to implement for a single unit often becomes a box of unending nightmares when you try to incorporate it into a product. Especially something as safety critical as throttle control above idle.
That said, I’m using an RC servo to control the throttle on my dynamometer.
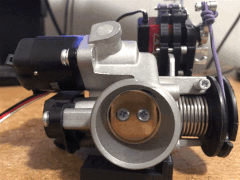
1 Like
I see what you are saying but there are ways to implement safety, I did think of that but I’m semi more interested in this project for my array or RC engines, even the smallest MS or Speeduino is too big for an RC model.
The PWM input and makes it simple for RC I could split the servo signal and input it as TPS before the ECM and provide a 0-5v signal with a small PCB but it is another thing in the mix.
Safety features could be integrated by using the other sensors as a safety as if you know the throttle is off and the MAP/ RPM or 02 is out-side of spec based on a table you know the throttle is stuck open and you can kill the engine.
You could integrate the servo with a spring and it what they do with RC throttles, to be honest I have not seen a throttle without a return spring except on RC and the engines with them fitted are very small and overcome the static friction on the servo.
As fer certification I don’t think RC requires it or any of the Chinese ATV’s coming into the country are certified in any way.
I did see that vibration on servos can damage the positioning POT but some of the modern ones have solid state hallefect/ inductive positioning control and some are even created to meet MIL spec for vibration and shock resistance like this one:
ProModeler - Servo, DS75CLHV #DS75CLHV
some servos have biderectional Comms and send a 50us pulse on the control wire for servo sync and out put their position as feed back to the transmitter for servo sync so you can read the position and error.
glumb/feedback-servo: DOMAN digital position feedback servo example code (github.com)